FEM Foundations (previously known as “Facility Preview”) was introduced starting in 2020 Higg FEM. From 2021 Higg FEM onwards, FEM Foundations, a subset of the full Higg FEM set of questions, becomes available for both self-assessment and verified-assessment on platform. FEM Foundations complements Higg FEM, enabling companies to quickly identify opportunities and hotspots in their extended value chain, as well as allowing new facility users to focus on FEM Foundations before moving to Higg FEM.
What is FEM Foundations?
FEM Foundations enables quick assessment of a facility’s environmental sustainability readiness, and offers an introductory step towards Higg FEM, speeding up the initial environmental sustainability assessment process. FEM Foundations only consists of a subset of Level One questions in the Higg Facility Environmental Module (Higg FEM). By using FEM Foundations, facilities new to the Higg Index can gradually become acquainted with the Higg Index as they prepare for the comprehensive Higg FEM assessment.
FEM Foundations does not provide a comprehensive view of value chain performance, it is an entry point, and it does not replace the Higg FEM assessment. It is highly encouraged for facilities to review all the questions within the module before getting started to understand the type of information and data the facilities will need to input into the module.
Please note that the FEM Foundations is NOT SCORED. This means that you do not get points. Please also note that the Higg Index benchmarking feature does not apply to FEM Foundations.
Note: Not all facilities are eligible to complete FEM Foundations. This assessment only applies to new facility accounts, meaning those facilities have not completed Higg FEM previously. Facilities that had completed a Higg FEM in previous cadence(s) or currently completing Higg FEM in the reporting year will not have accessibility to the FEM Foundations.
How Does FEM Foundations Work:
FEM Foundations works similarly to Higg FEM. A self-assessment of FEM Foundations must be completed and posted before verification can begin. Once a module is posted and shared, your shared account will be able to view your completed module.
A facility should complete and post either one FEM Foundations or one Higg FEM in the same FEM cadence year. Unlike Higg FEM, FEM Foundations does not have a reporting period, it is available all year round, and it measures performance from the most recent 12-months. For example, if the facility is completing FEM Foundations in May 2022, FEM Foundations measures performance from May 2021 to April 2022).
How Does Verification work on FEM Foundations:
Verification on the FEM Foundations has the same workflow and verification protocol as the Higg FEM. While the majority of the questions in FEM Foundations are identical to questions in Higg FEM, thus verification criteria will be the same for those questions. There are some exceptions. For those questions that are not identical, please refer to the verification guidance in this guide.
For general Verification protocol, please refer to https://howtohigg.org/higg-fem-verification-program/fem-verification-protocol/ .
How To Read This Guide:
This guide will provide a quick access to full guidance for completing FEM Foundations. All questions in FEM Foundations are also in Higg FEM. In many cases, this guide provides direct links to the 2021 How to Higg FEM Guide, because many FEM Foundations questions and verification criteria are identical to the Higg FEM.
For FEM Foundations questions that are not identical, the guidance specific to FEM Foundations is provided in this Appendix.
The table below indicates the Higg FEM questions that are included in FEM Foundations. Questions that are highlighted in Yellow indicate questions that have been modified to reflect foundational practices in a facility (e.g. FEM inputs or data requirements).
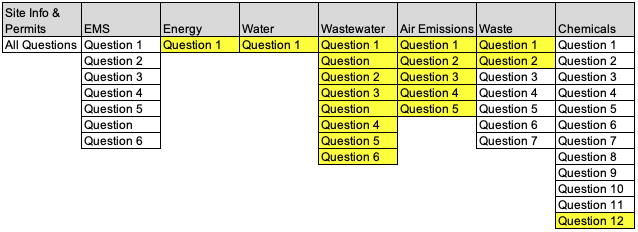
Facility Site Info & Permits
The questions in Facility Site Info & Permits are the same across full Higg FEM and Facility Foundations. Please refer to the FEM2021 How to Higg Guide Guide for full guidance.
Reference: FEM2021 How to Higg Guide – Facility Site Info & Permits section
EMS
This question is the same across full Higg FEM and Facility Foundations. Please refer to the FEM2021 How to Higg Guide for full guidance.
Reference: FEM2021 How to Higg Guide – EMS section
This question is the same across full Higg FEM and Facility Foundations. Please refer to the FEM2021 How to Higg Guide for full guidance.
Reference: FEM2021 How to Higg Guide – EMS section
This question is the same across full Higg FEM and Facility Foundations. Please refer to the FEM2021 How to Higg Guide for full guidance.
Reference: FEM2021 How to Higg Guide – EMS section
This question is the same across full Higg FEM and Facility Foundations. Please refer to the FEM2021 How to Higg Guide for full guidance.
Reference: FEM2021 How to Higg Guide – EMS section
This question is the same across full Higg FEM and Facility Foundations. Please refer to the FEM2021 How to Higg Guide for full guidance.
Reference: FEM2021 How to Higg Guide – EMS section
This question is the same across full Higg FEM and Facility Foundations. Please refer to the FEM2021 How to Higg Guide for full guidance.
Reference: FEM2021 How to Higg Guide – EMS section
This question is the same across full Higg FEM and Facility Foundations. Please refer to the FEM2021 How to Higg Guide for full guidance.
Reference: FEM2021 How to Higg Guide – EMS section
Energy
This question has been modified to suit foundation practices in a facility. Hence it will not resemble the corresponding question in full Higg FEM. Please refer to the guidance below to meet verification requirements for this question.
What is the intent of the question?
The intent is to help you build your facility’s energy source list, which provides a clear understanding of what energy is being used, where it is being used in your factory, and how much is being used.
Measurement of energy use from all sources is the foundation of energy management and the overall sustainability program for a company. Measurement of all energy sources allows you to analyze your biggest energy drivers, detect any abnormal consumption, set energy reduction targets, and measure GHG emissions.
Technical Guidance:
Please include all energy used within the site’s physical boundary and operations under your business control (owned, operated or directly leased). Please exclude any outsourced services or areas such as a contracted canteen or rental shop.
Energy use tracking is considered the first step in managing energy use. When establishing your energy tracking and reporting program, start by doing the following:
- Map out business and operational processes to identify sources of energy use.
- Note: Energy consumed by facilities or tenants on-site that are NOT owned or controlled by your facility should be excluded for your energy reporting in the Higg FEM. For example, energy consumed by an onsite canteen/food service provider that is not owned or controlled by your facility should be excluded.
- Establish procedures to collect and track energy use data:
- Use utility bills to determine the quantity of purchased electricity, steam and heat used.
- Track other fuels used for onsite energy generation such as diesel in generators and coal in boilers owned or controlled by the facility.
- Track fuels used for mobile combustion sources owned or controlled by the facility such as private cars and fork lifts.
- Install sub-meters to track the amount of renewable energy generated, if renewable energy is generated in-house.
- Record tracking data (e.g. daily, weekly, monthly consumption records) in a format that is easy to review [e.g. spreadsheet (e.g. Microsoft Excel) or similar data analytics program that allows export of data in a human readable format (e.g. Excel, csv)] and maintain relevant supporting evidence for review during verification.
How This Will Be Verified:
- Documentation Required:
- Frequency and method of measurement for all sources of energy
- Electricity, fuel, steam and other energy consumption records (e.g. monthly bills and annual consumption records; metering records compiled in a spreadsheet (e.g. Excel) is ok as long as the metering records are available for review as well) whose totals match the reported answers to all questions answered.
- Interview Questions to Ask:
- Discussion with Management:
- Management is aware of laws and regulations, where applicable, concerning energy use, transport and GHG emissions?
- Management provides the appropriate resources to ensure that applicable laws and regulations are maintained?
- Is the facility meeting local requirements regarding energy consumption and documentation?
- Discussion with Management:
- Inspection – Things to Physically Look For:
- Onsite meters
- Equipment related to energy (production or energy consuming)
- Maintenance (appears to be well maintained?)
Water
Please refer to the FEM2021 How to Higg Guide for full guidance on applicability of this section
Reference: FEM2021 How to Higg Guide – Water section
This question has been modified to suit foundation practices in a facility. Hence it will not resemble the corresponding question in full Higg FEM. Please refer to the guidance below to meet verification requirements for this question.
Please note that if you are unable to identify the sources of water used, please select “Water – general or unknown origin” as your answer for this question.
What is the intent of the question?
The intent is to help you build your facility’s water source list, which provides a clear understanding of what water is being used, where it is being used in your factory, and how much is being used.
Measurement of all freshwater use from all freshwater sources is the foundation of a water management. Ensuring measurement of all freshwater sources gives facilities the ability to perform a water balance, set freshwater based key performance indicators (KPI), identify water leaks, and establish and measure freshwater footprint. It is recommended that water be measured monthly or more frequently (e.g. onsite meter readings).
The most common freshwater use is potable municipal or city water (drinking water). Other sources can be from ground water wells, surface waters (lakes, rivers, and streams), rain water, recycled process water, and even condensate when collected from steam which is supplied to the business from an external source.
Technical Guidance:
Please include all water sources used within the site’s physical boundary and operations under your business control (owned, operated or directly leased). Please exclude any outsourced services or areas such as a contracted canteen or rental shop.
Water use tracking is considered the first step in managing water use. It’s recommended to start by:
- Mapping out business and operational processes to identify water sources, areas/processes that consume water.
- Establish procedures to collect and track water use data:
- Use utility bills to determine the quantity of purchased water
- Determine methods to track water consumption from other applicable sources, such as rainwater, recycled water, etc.
- Install sub-meters to track the amount of water used on-site.
- Record tracking data (e.g. daily, weekly, monthly consumption records) in a format that is easy to review [e.g. spreadsheet (e.g. Microsoft Excel) or similar data analytics program that allows export of data in a human readable format (e.g. Excel, csv)] and maintain relevant supporting evidence for review during verification.
How This Will Be Verified:
- Documentation Required:
- Water consumption records (e.g. monthly bills and annual consumption records; metering records compiled in a spreadsheet (e.g. Excel) is ok as long as the metering records are available for review as well) whose totals match the reported data to all questions answered.
- Meter calibration records where applicable (e.g. as per manufacturer’s specifications).
- Estimate methodology documented where applicable
- Inspection – Things to Physically Look For:
- Confirm sources of water intake and/or extraction
- If a facility has flow meters, see if the flowmeters are in place and working
Wastewater
Please refer to the FEM2021 How to Higg Guide for full guidance on applicability of this section.
This question has been modified to suit foundation practices in a facility. Hence it will not resemble the corresponding question in full Higg FEM. Please refer to the guidance below to meet verification requirements for this question.
Industrial: include all manufacturing and/or commercial activities within your facility site such as industrial processing, lubrication, maintenance etc.
Domestic: include all domestic wastewater generation including wastewater/effluent from dormitories, bathrooms, showers, and kitchens, etc.
What is the intent of the question?
The intent of this question is to ensure that the site knows how much wastewater is being produced and where it is discharged to. This information can be derived from the facility’s water balance. By answering this question, facilities can demonstrate how they monitor and manage wastewater volume. Knowing your volume is an important first step to making decisions on appropriate treatment options.
Wastewater tracking allows complete visibility into daily operations of a facility and what operations impact wastewater volumes. Knowing your wastewater volume is directly linked to ecological impact and operational costs.
Technical Guidance:
Wastewater tracking should include both domestic and industrial wastewater where applicable and include water that is either discharged, reclaimed/recycled or reused at your site, that is generated from all manufacturing and/or commercial activities within your facility.
When tracking wastewater, it’s recommended to start by:
- Mapping out facility areas and processes to identify where wastewater is generated and discharged.
- Establish procedures to collect and track wastewater data:
- Install on-site meters or use metered invoices from off-site treatment facilities.
- If estimation techniques are used to determine the amount of wastewater generated, the calculation methodology should be clearly defined.
- Record tracking data (e.g. daily, weekly, monthly records) in a format that is easy to review [e.g. spreadsheet (e.g. Microsoft Excel) or similar data analytics program that allows export of data in a human readable format (e.g. Excel, csv)] and maintain relevant supporting evidence for review during verification.
Additional guidance on measuring and estimating wastewater volume can be found in the FEM2021 How to Higg Guide – Wastewater section
How This Will Be Verified:
- Documentation Required:
- Wastewater discharge records (e.g. monthly bills and annual discharge records; metering records compiled in a spreadsheet (e.g. Excel) is ok as long as the metering records are available for review as well).
- Meter calibration records where applicable (e.g. as per manufacturer’s specifications).
- Inspection – Things to Physically Look For:
- Is wastewater/effluent directed to a wastewater/effluent treatment plant or does it undergo treatment prior to discharge?
- Are surface water/storm water drains free from contamination and blockages?
- Are procedures established to manage wastewater/wastewater discharges being followed? (e.g. management of wastewater, activities etc.)
- Are spills or leaks to the environment observed?
- Are there boiler blow down and other membrane cleaning activities where water is collected and tracked as well?
- Are the flowmeters in place working (in case the facility has selected the “meters” method), calibrated and accessible?
The following question is applicable only for facilities that generate industrial wastewater.
This question is the same across full Higg FEM and Facility Foundations. Please refer to the FEM2021 How to Higg Guide for full guidance.
The following question is applicable only for facilities that utilize an offsite wastewater treatment plant.
This question is the same across full Higg FEM and Facility Foundations. Please refer to the FEM2021 How to Higg Guide for full guidance.
The following question is applicable only for facilities that generate industrial wastewater.
This question is the same across full Higg FEM and Facility Foundations. Please refer to the FEM2021 How to Higg Guide for full guidance.
The following question is applicable only for facilities that generate industrial wastewater.
This question is the same across full Higg FEM and Facility Foundations. Please refer to the FEM2021 How to Higg Guide for full guidance.
The following question is applicable only for facilities that generate industrial wastewater that is treated on-site.
This question is the same across full Higg FEM and Facility Foundations. Please refer to the FEM2021 How to Higg Guide for full guidance.
The following question is applicable only for facilities that generate domestic wastewater that is treated on-site.
This question is the same across full Higg FEM and Facility Foundations. Please refer to the FEM2021 How to Higg Guide for full guidance.
The following question is applicable only for facilities that treat wastewater using septic.
This question is the same across full Higg FEM and Facility Foundations. Please refer to the FEM2021 How to Higg Guide for full guidance.
Air Emissions
Please refer to the FEM2021 How to Higg Guide for full guidance on applicability of this section.
Reference: FEM2021 How to Higg Guide – Air emissions section
The following question is applicable only for facilities that have sources of air emission from operation.
This question has been modified to suit foundation practices in a facility. Hence it will not resemble the corresponding question in full Higg FEM. Please refer to the guidance below to meet verification requirements for this question.
What is the intent of the question?
The intent of this question is to drive you to inventory all possible sources of emissions to air from operations on-site.
Technical Guidance:
Air quality standards: Facilities should not have emissions that result in pollutant concentrations that reach or exceed relevant ambient quality guidelines or contribute a significant portion to the attainment of relevant ambient air quality guidelines. Some countries utilize ground level concentration measurements for regulatory assessment (permitting).
Emission standards (concentration): Air pollution limits are sometimes concentration limits (e.g. ppm, mg/m3). Regulatory authorities may set maximum emissions concentrations based upon overall goals to reduce air pollution. For example, for automobiles, governments may regulate concentration limits measured at the exhaust.
Emissions standards (quantity): Air pollution limits may also be measured by the actual quantity of emissions from a source. Some regulatory authorities limit the annual quantity of emissions from a whole facility, however, others apply to point source emissions that are specifically defined or identified by regulation or other requirements.
Regulatory requirements for monitoring of emissions varies depending on local regulatory requirements. Annual quantities of emissions from variable sources may also need to be determined using engineering estimates or modelling based on the process inputs (e.g. the amount and types of chemicals used in the process).
Creating an Air Emissions Inventory:
An air inventory is needed for the facility to track and manage emissions and their sources. To prepare a facilities inventory, emissions from all ancillary activities and equipment should be included. Regular review should be carried out to make sure the inventory is up-to-date. This inventory should include emissions sources regulated by permit as well as those not currently regulated.
The following elements are suggested to be included in the inventory (source: GSCP):
- Pollutants known or likely to be present
- Quantity of each pollutant emitted
- Emissions/discharge points
- Control devices and their operating parameters
- Frequency of monitoring
- Compliance with legal regulations
An example inventory can be downloaded here: https://www.sumerra.com/wp-content/uploads/Air-Emissions-Inventory.xlsx
Emission testing (concentration): Emissions testing is sometimes regulated by concentration, which requires certain test locations to fall below a given emissions per time. Testing shall be done during representative operating scenarios, and non-standard testing or calculations can be considered separately. Each test method and/or equipment used to determine emissions likely has a minimum time and/or repeat test requirement, and these statistical variations shall be considered.
Multiple discharge points from a type of emissions source (e.g. boilers or multiple solvent application processes) can be considered a single emissions source for the purposes of reporting, or may be separated by each location.
How This Will Be Verified:
- Documentation Required:
- An inventory of emissions to air for ALL sources related to facility operations.
- Emission testing/monitoring reports. Testing data compiled in a spreadsheet (e.g. Excel) is ok as long as the testing reports are available for review
- Inspection – Things to Physically Look For:
- Onsite evaluation of air emission sources listed.
- Ensure all applicable equipment is listed on sources list.
The following question is applicable only for facilities that have sources of air emission from production.
This question has been modified to suit foundation practices in a facility. Hence it will not resemble the corresponding question in full Higg FEM. Please refer to the guidance below to meet verification requirements for this question.
What is the intent of the question?
The intent of this question is for your facility to know the sources of process air emissions to put necessary action and abatement in place to monitor and control them.
Technical Guidance:
All process emissions should be tracked, regardless of if they are captured and discharged in a stack/chimney. These may include non-point sources such as drying rooms, or fugitive emissions such as outdoor dust.
The following elements are suggested to be included in the inventory (GSCP):
- The pollutants known or likely to be present
- Emissions/discharge points or locations, if applicable
- Compliance with legal regulations, if applicable
Non-point source emissions may require a different methodology to determine the amount of pollutants emitted. Additional explanation and examples of how air emission can be determined are listed below:
- Inventory-based (Potential to Emit, PTE)
- A Potential To Emit looks at inventories for all air emissions including energy generation and process chemistry to establish the maximum amount that could be emitted from that facility.
- Inventory-based (Potential to Emit + Mass Balance and/or Abatement)
- Once a PTE analysis is completed, mass balance and/or abatement assumptions may be added.
- Emissions Factor-based (Factory or Offsite Testing)
- Emissions factors represent standard rates of emissions given a certain process. These types of testing may be done onsite or offsite by a 3rd party. Please note that the general recipe and tool must be the same or similar enough to generate the same emissions for this factor to be used. Sometimes, for a given facility, hundreds or even thousands of emissions factors are needed to represent their operations. All testing and documentation must be available to utilize this method. Where recipes and tool designs do not change frequently, or when similar recipes are used over a long time, this may be a very cost effective way to estimate emissions to prevent repetitive emissions testing.
The chosen emission estimation method must be applicable to the source type (e.g. for intermittent activities or high change over with different chemistries the quantity could be estimated based on consumption of solvents annually for that process).
Mass Balance Example: Emissions may be estimated based on the chemical composition of materials used (i.e. percentage of VOC content or individual pollutant) and how much of the chemical is used annually (i.e. liters/year).
How This Will Be Verified:
- Documentation Required:
- An inventory of emissions to air for ALL sources of emissions from production processes.
- Emission testing/monitoring reports. Testing data compiled in a spreadsheet (e.g. Excel) is ok as long as the testing reports are available for review
- Inspection – Things to Physically Look For:
- Ensure all applicable equipment is listed on sources list
- Supporting documentation for test results for all sources of emissions (equipment) for those regulated by a governmental/ accredited agency
Additional guidance on tracking air emissions can be found in the FEM2021 How to Higg Guide – Air Emissions section
The following question is applicable only for facilities that have refrigerants of air emission.
Do you track refrigerant use/emissions?
This question has been modified to suit foundation practices in a facility. Hence it will not resemble the corresponding question in full Higg FEM. Please refer to the guidance below to meet verification requirements for this question.
Having to add refrigerants to existing equipment indicates the system has a leak.
ONLY answer NO if you did not add additional refrigerants to any existing equipment in the reporting year.
If you do not know whether refrigerants were added to any existing equipment in the reporting year, you should answer Unknown.
If you know that refrigerants were added, however you do not know the quantity, You should select Yes to the question “Did your facility add additional refrigerants to any existing equipment in the reporting year?”, and select No to the Question “Do you track refrigerant use/emissions?”
What is the intent of the question?
The intent of this question is to help you identify what refrigerants are being used, where they are being used in your factory, and how much is potentially being emitted to the atmosphere.
Technical Guidance:
Refrigerants are ozone depleting substances that can be harmful contributors to GHG emissions and climate change due to the relatively high global warming potentials (GWPs) common refrigerants have. Refrigerants are often emitted through equipment leaks, servicing and disposal.
Although most modern equipment is designed to minimize leaks, it is important to identify leaks if they do occur. Leaks are typically identified by having to add additional refrigerant to equipment. It is also important to have an action plan to fix the leaks and/or upgrade equipment to eliminate refrigerant leakage.
If refrigerants are used on-site, solutions to phase out these gases should be considered. One other solution is to use refrigerants with lower global warming potentials (GWP) such as HFO’s in the applications of refrigerants, aerosol propellants and foam blowing agents.
How This Will Be Verified:
- Documentation Required:
- All refrigerant equipment has a log of equipment servicing including refrigerant replacement that is kept up to date
- These records must show that no refrigerants were added during the last 12 months
- Inspection – Things to Physically Look For:
- Well-kept records of equipment maintenance
- Potential refrigerant leaks
The following question is applicable only for facilities that have sources of air emission from operation.
This question is the same across full Higg FEM and Facility Foundations. Please refer to the FEM2021 How to Higg Guide for full guidance.
Reference: FEM2021 How to Higg Guide – Air Emissions section
The following question is applicable only for facilities that have sources of air emission from production.
This question is the same across full Higg FEM and Facility Foundations. Please refer to the FEM2021 How to Higg Guide for full guidance.
Reference: FEM2021 How to Higg Guide – Air Emissions section
Waste
This question has been modified to suit foundation practices in a facility. Hence it will not resemble the corresponding question in full Higg FEM. Please refer to the guidance below to meet verification requirements for this question.
Includes non-hazardous production waste and domestic waste.
What is the intent of the question?
The intent is to build awareness of all non-hazardous waste types (both production and domestic waste) at your facility and to start tracking the volume each waste type generates. You must know your sources of waste before you can make strategic decisions on how to reduce and divert waste. It’s important to understand your current waste management practices and to prioritize improvements for the waste sources that you produce the most. By doing this you can find more effective alternatives to reduce and divert waste.
Technical Guidance:
Developing a waste inventory is considered the first step in waste management. When establishing your waste tracking and reporting program, start by doing the following, which applies to non-hazardous wastes covered in this question and hazardous waste tracking covered in Question 2:
- Map out business and operational processes to identify where waste is being generated and all the types of wastes that are generated.
- Establish procedures to collect and track waste data:
- Use on-site scales, waste invoices/manifests, receipts for waste materials that are sold, etc. to determine the amount of waste generated.
- Record tracking data (e.g. daily, weekly, monthly waste quantities) in a format that is easy to review [e.g. spreadsheet (e.g. Microsoft Excel) or similar data analytics program that allows export of data in a human readable format (e.g. Excel, csv)] and maintain relevant supporting evidence for review during verification.
How This Will Be Verified:
- Documentation Required:
- List of ALL non-hazardous waste produced by the facility
- Production Waste
- Packaging waste
- Domestic Waste
- Records for tracking both the quantity and type of disposal (including disposal destination) of ALL non-hazardous waste (e.g. invoices from waste contractors, weighing records compiled in a spreadsheet (e.g. Excel) is ok as long as supporting evidence is available for review as well).
- All non-hazardous waste sources at the facility are tracked in full.
- List of ALL non-hazardous waste produced by the facility
- Inspection – Things to Physically Look For:
- Sources of non-hazardous waste production
- Equipment for waste quantity measurement
- Collection sites for waste disposal
This question has been modified to suit foundation practices in a facility. Hence it will not resemble the corresponding question in full Higg FEM. Please refer to the guidance below to meet verification requirements for this question.
What is the intent of the question?
The intent is to build awareness of all hazardous waste types produced onsite and to track the volume of each waste type generated and the method of disposal. You must know your sources of waste before you can make strategic decisions on how to reduce, divert or improve waste management.
Technical Guidance:
Because of its hazardous characteristics, all hazardous waste must be well tracked and controlled to meet the local laws & regulations. To identify your hazardous waste, each country has its own National Hazardous Waste Inventory and National Hazardous Waste Identification Standard. Please refer to these standards and inventory.
Hazardous waste poses a greater risk to the environment and human health than non-hazardous waste, and thus requires a stricter management process.
It is important to also specify how each waste stream is being disposed of in order to meet the local laws and regulations regarding hazardous waste and identify opportunities to improve the disposal methods (e.g., reduce, recycle and incinerate with energy recovery).
It is advisable for your factory to regularly check that hazardous wastes are being properly handled and are treated/ disposed of at the approved intended facility.
An example of contaminated materials can be a piece of cotton or nylon used to clean machines. The fabric is contaminated by hydraulic oil or lubricant oil or ink or chemicals and may be classified as hazardous waste.
Note: The classification into hazardous and non-hazardous waste may differ from one country legislation to another that may define which ‘waste’ are categorized as hazardous differently. The facility should follow the legal waste requirements. If legal requirements are not available, select more stringent industry guidelines.
How This Will Be Verified:
- Documentation Required:
- List of ALL hazardous waste produced by the facility
- Production Waste
- Packaging waste (e.g. chemical drums and containers)
- Domestic Waste
- Records for tracking both the quantity and type of disposal (including disposal destination) of ALL hazardous waste (e.g. invoices from waste contractors, weighing records compiled in a spreadsheet (e.g. Excel) is ok as long as supporting evidence is available for review as well).
- Permits for hazardous waste handling (if applicable)
- All hazardous waste sources at the facility are tracked in full.
- List of ALL hazardous waste produced by the facility
- Inspection – Things to Physically Look For:
- Sources of hazardous waste production
- Collection sites for waste disposal
This question is the same across full Higg FEM and Facility Foundations. Please refer to the FEM2021 How to Higg Guide for full guidance.
Reference: FEM2021 How to Higg Guide – Waste section
This question is the same across full Higg FEM and Facility Foundations. Please refer to the FEM2021 How to Higg Guide for full guidance.
Reference: FEM2021 How to Higg Guide – Waste section
This question is the same across full Higg FEM and Facility Foundations. Please refer to the FEM2021 How to Higg Guide for full guidance.
Reference: FEM2021 How to Higg Guide – Waste section
This question is the same across full Higg FEM and Facility Foundations. Please refer to the FEM2021 How to Higg Guide for full guidance.
Reference: FEM2021 How to Higg Guide – Waste section
This question is the same across full Higg FEM and Facility Foundations. Please refer to the FEM2021 How to Higg Guide for full guidance.
Reference: FEM2021 How to Higg Guide – Waste section
Chemical Management
Please refer to the FEM2021 How to Higg Guide for full guidance on applicability of this section
Reference: FEM2021 How to Higg Guide – Chemical Management section
This question is the same across full Higg FEM and Facility Foundations. Please refer to the FEM2021 How to Higg Guide for full guidance.
Reference: FEM2021 How to Higg Guide – Chemical Management section
This question is the same across full Higg FEM and Facility Foundations. Please refer to the FEM2021 How to Higg Guide for full guidance.
Reference: FEM2021 How to Higg Guide – Chemical Management section
This question is the same across full Higg FEM and Facility Foundations. Please refer to the FEM2021 How to Higg Guide for full guidance.
Reference: FEM2021 How to Higg Guide – Chemical Management section
This question is the same across full Higg FEM and Facility Foundations. Please refer to the FEM2021 How to Higg Guide for full guidance.
Reference: FEM2021 How to Higg Guide – Chemical Management section
This question is the same across full Higg FEM and Facility Foundations. Please refer to the FEM2021 How to Higg Guide for full guidance.
Reference: FEM2021 How to Higg Guide – Chemical Management section
This question is the same across full Higg FEM and Facility Foundations. Please refer to the FEM2021 How to Higg Guide for full guidance.
Reference: FEM2021 How to Higg Guide – Chemical Management section
This question is the same across full Higg FEM and Facility Foundations. Please refer to the FEM2021 How to Higg Guide for full guidance.
Reference: FEM2021 How to Higg Guide – Chemical Management section
This question is the same across full Higg FEM and Facility Foundations. Please refer to the FEM2021 How to Higg Guide for full guidance.
Reference: FEM2021 How to Higg Guide – Chemical Management section
This question is the same across full Higg FEM and Facility Foundations. Please refer to the FEM2021 How to Higg Guide for full guidance.
Reference: FEM2021 How to Higg Guide – Chemical Management section
The following question is applicable only for facilities that use chemicals in the production process.
This question is the same across full Higg FEM and Facility Foundations. Please refer to the FEM2021 How to Higg Guide for full guidance.
Reference: FEM2021 How to Higg Guide – Chemical Management section
The following question is applicable only for facilities that use chemicals in the production process.
This question is the same across full Higg FEM and Facility Foundations. Please refer to the FEM2021 How to Higg Guide for full guidance.
Reference: FEM2021 How to Higg Guide – Chemical Management section
The following question is applicable only for facilities that use chemicals in the production process.
This question has been modified to suit foundation practices in a facility. Hence it will not resemble the corresponding question in full Higg FEM. Please refer to the guidance below to meet verification requirements for this question.
What is the intent of the question?
The intended behavior for this question is for facilities to understand MRSLs, which should be used to enable compliant chemical purchases and chemical inventory within the facility, its contractors and subcontractors. The process should be formally documented in some written form and updated on an annual basis.
MRSL is important because a facility that uses compliant chemicals, in accordance with technical specification directions, has better environmental outcomes for the various facility discharges and more consistent RSL material compliance.
Technical Guidance:
For all products which are considered to be MRSL compliant, there must be an appropriate process for validating the MRSL present in the facility.
How This Will Be Verified:
- The facility or its parent/corporate group can demonstrate a well-documented (written) chemical review process that monitors, updates and shows compliance to legislations, customer MRSL requirements
- The process should also demonstrate how chemicals are reviewed / checked against the MRSL prior to purchase.
Documentation Required:
- Chemical Inventory List (CIL)
- Chemical review policy and process flow
- List of non-conforming chemicals
- MRSLs applicable to the facility e.g. own MRSL, customers’ MRSL, or ZDHC MRSL
- Positive lists from chemical suppliers
- Letter of compliance to MRSL with chemical name, date of issuance, and test reports
Inspection – Things to Physically Look For:
- A visual verification of several work processes for use of chemicals or materials against the supplied inventory list.